STEP 5
This is Step 5 of the 6 steps to get started — learn how to work with case studies.
WORK INDIVIDUALLY AT FIRST, not in groups. Start with the THREE CHALLENGES in the Cincinnati Seasonings online introduction. Each person needs their own account. By working individually people learn to use the simulation software, and learn how to think about supply chains as combinations of the four entities (products, facilities, vehicles, and routes). After working through the three challenges of Cincinnati Seasonings, people will have the skills needed to work on more advanced cases, and to work in groups!
IMPROVE SUPPLY CHAIN PERFORMANCE — Work with Case Studies to Build Real World Supply Chain Skills
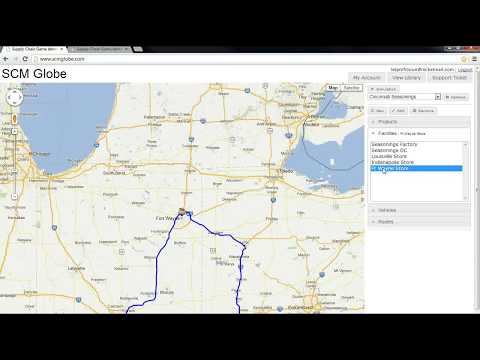
Simulations find problems and identify areas for improvement in your supply chain. Apply what you learn in your class and what you already know about supply chains to fix problems found in the simulations. Go with your best guess; try out different ideas. Simulations will show how well they work. Solutions that work well in these simulations will also work well in real supply chains.
There is a collection of case studies available in the SCM Globe Library. Each case explores a different set of supply chain issues. If you have an active account, you can access any or all of these cases. Find out about them by going to the “Supply Chain Case Studies” section of this online guide (see Table of Contents on right side of this webpage). Click on the case studies listed there and read their online introductions. For each case there is a Case Study Concept at the beginning of the introduction summarizing the issues explored in that case. Read the full online introduction for a case when you start working with it.
Access the case study library from your Account Management screen by clicking on the “View Library” button (1) in the upper right corner of the account management screen as shown below. The Library window opens and you can see a list of supply chain models (2). Click the “Import” button next to a desired supply chain, give it a name and click the “Save” button. This saves a copy of that supply chain into your account. Import as many supply chains as you wish. Click the “My Account” button (3) to go back to your Account Management screen.
From your Account Management screen click the “Edit” or the “Simulate” button next to the supply chain you want to work with.
Exploring a Central Supply Chain Challenge
Cincinnati Seasonings explores a critical challenge for any supply chain: Meet product demand (be responsive) while also reducing inventory and operating costs (be efficient). It uses a relatively simple supply chain composed of one factory, one distribution center (DC), and three stores. As the case study progresses, you are challenged to add more stores and expand the supply chain to support the company’s growth. As you do this, you’ll need to find ways to keep operating costs and inventory levels as low as possible while still meeting customer demand at a growing number of stores.
Most companies have annual budgets along with strategic revenue and operating goals, but they do their operations planning on a monthly basis. Every month the company updates its product demand forecasts at the stores, and that leads to changes in its production schedule at the factory. Which in turn leads to changes in vehicles and delivery routes. This is why you focus on 30-day simulations. Cincinnati Seasonings uses a 30-day sales and operations planning (S&OP) process. Your job as supply chain manager at Cincinnati Seasonings is to plan and manage supply chain operations from one monthly S&OP cycle to the next. Your goal is to meet product demand each month at all the stores (be responsive) while also reducing inventory and operating costs as much as possible (be efficient).
In this case study you learn about the basics of setting up a supply chain and managing its daily operations. You create facilities, vehicles and routes needed for different supply chain designs to respond to different challenges. And you run simulations that show how well your designs work. Based on what the simulations show, you keep improving your design to get the best performance. In this process, you gain an appreciation for some of the key challenges involved in operating any supply chain.
When you import a copy of the Cincinnati Seasonings supply chain into your account you can click on the “Edit” button next to it in your account management screen. When you do this it will open up the model of the supply chain in the Edit screen as shown below. When you first load the Edit or Simulate screens the full supply chain sometimes does not appear on the map or the screen remains blank — click browser refresh to redraw the screen
In the Edit screen you can inspect the model and make any changes you want. Then you click on the “Simulation” button in the upper right corner of the Edit screen and it opens the Simulate screen in another browser tab next to the Edit screen browser tab. When you click on the “Play” button in the Simulate screen the Cincinnati Seasonings simulation cycles through two days and then it finds a problem — a store has run out of storage space for its products. Now you make decisions on how to fix this problem.
See short video clips illustrating how to create and edit facilities, vehicles, and routes – scroll down to “Q&A VIDEO BOOK” at the bottom of this page.
There is No Single “Right Answer”
You have many options for fixing problems and some work better than others (just like the real world). Apply supply chain principles and best practices learned from your readings and course lectures. For example, when working with the Cincinnati Seasonings supply chain, the first problem you will encounter is at the end of day two when the Ft Wayne store runs out of storage space. You can increase the storage space at the store, or deliver less to the store, or any combination of those two. Look at the information available in the data displays on the right side of the Simulate screen to get ideas about what to do. When you fix one problem, the simulation will find other problems, such as running out of products at a different store as shown in the screenshot below.
You will see that sometimes a solution to one problem causes other problems to occur. As you work with any of the cases and respond to the problems that arise, you see how the four entities (products, facilities, vehicles, routes) interact with each other, and you learn how to co-ordinate their operations so as to get good overall supply chain performance.
To fix problems found in simulations, go to the first browser tab — the Edit Screen, and make changes to the supply chain model. Click on “Facilities”; and highlight the facility where a problem occurs. Or select the Vehicle or Route that you want to change. A dialog box for that entity appears, and you can click on the numbers in order to edit them. You may want to increase storage capacity at the facility, or you might change replace a small truck with a large truck. Or increase or reduce delivery amounts (drop qty) of products to a facility (a stop) on a delivery route. You may want to adjust factory production rates and delivery schedules (delay between departures) for vehicles. Take whatever actions you think are needed. You will see some actions work better than others (remember to click the “Update” button in entity dialog boxes when you make changes).
Then go back to the second browser tab — the Simulate Screen, and run a simulation. Click the browser refresh button or the “Reload Supply Chain” button to incorporate the changes you just made. Then click “Play” to run the simulation again. Depending on the changes you make, your supply chain simulation will run for additional days, and other problems will arise. Do whatever you feel you need to do to get the simulation to run for 30 days (as you make changes to your supply chain the Butterfly Effect will cause your simulation results to differ somewhat from others working on the same case study).
Click on Browser Tabs to Move between Edit and Simulate Screens
Flip back and forth between Edit and Simulate by clicking on the browser tab with the screen you want (as shown below). Click “My Account” button on either the Edit or Simulate screens to return to your Account Management screen. Click the blue “Help” button on any screen to open a third tab with the Online Guide.
The best way to explore and find good solutions is to go back and forth — edit your supply chain then simulate the results. Simulations show points of failure in the supply chain and provide data you can use to fix those problems. Edit the supply chain model to fix the problems. Then run the simulation again. Continue this iterative process until you get a supply chain model that performs well.
Click browser refresh to redraw your supply chain on the map in the Edit screen. As you edit one route, other routes will disappear. If you want to see all the routes again, click browser refresh.
In Cincinnati Seasonings and in other case studies, once you stabilize a supply chain by getting it to run for 30 days, you are then challenged to extend and adapt your supply chain to respond to new events such as expanding to support new stores, moving to a different mode of transportation, or opening a new distribution center. The simulations accurately model real supply chains, so solutions that handle challenges in the case studies will also handle similar challenges in real supply chains. Companies use SCM Globe to create models and simulations of their actual supply chains and explore options for improvement. What works well in the simulations also works well in the real world.
As you work through the three challenges in the online introduction to Cincinnati Seasonings, you will gain an understanding of how supply chains operate, and develop analytical skills to evaluate different options for improving their performance. The First Challenge is first to get the supply chain to run for 30 days. The Second Challenge is to add two new stores and still keep the supply chain running for 30 days. And the Third Challenge is to keep the expanded supply chain running for 30 days, and also reduce the operating costs and amounts of on-hand inventory so the company can earn a profit.
A Few Things You SHOULD NOT Do
SCM Globe is used to model and simulate real supply chains so all numbers in any model can be changed as needed to more accurately describe actual products, facilities, vehicles and routes. However, when using the simulations as a learning tool in a case study it does not make sense to change some default values even though the software will let you do so. You should not change certain default values listed below because it either doesn’t make business sense, or it doesn’t make logistics sense (see further explanation in the email a logistics professor sent to his students — Case Study Caveats and Taboos):
- Don’t reduce product demand or prices – that makes no business sense as business is about increasing demand and profits.
- Don’t increase or decrease initial on-hand inventory amounts at the start of a case study – that makes no logistics sense as inventory doesn’t simply appear or disappear.
- Don’t change default values for daily rent and operating costs at facilities, or default values for vehicle operating costs. Unless your instructor says otherwise, you can assume they are out of your control in this case study.
- NOTE: Default rent costs at facilities are set higher than current market rates. If your instructor does allow you to change rent costs, use a commercial real-estate website such as CityFeet (www.cityfeet.com) to research current rental rates in different cities and type in those rental rates in place of the default rates.
Apart from these few things, you can do anything else to address challenges and solve problems that arise in the simulations. You can:
- add or change types of delivery vehicles and delivery routes
- change delivery frequencies (delay between departures)
- change delivery amounts (drop qty)
- expand or reduce storage capacity at facilities
- change production rates at the factory
- experiment with different locations for new facilities added during the case study
- You can do anything not specifically prohibited!
The case studies are not multiple choice tests. There is no single “right answer” — only better answers. Running simulations and downloading the results to create Profit & Loss Reports will show you the better answers. They are the ones that keep the supply chain running for 30 days at lower operating costs and lower inventory levels — they make the supply chain as responsive and efficient as possible.
Simulations Generate Lots of Performance Data
Use this data in refining your supply chain model. Learn more about using simulation data in “Analyzing Simulation Data“. Apply supply chain principles and practices that you learn in course reading and lectures to solve the problems you encounter. Try different courses of action and run simulations to see what works best. Be creative. In the process you will come to understand a lot about supply chains, and you can use what you learn to solve problems in real supply chains.
Once you get your simulation to run for 30 or more days you can download the simulation data to a reporting template and produce monthly Profit & Loss reports plus key performance indicators (KPIs) such as the example shown below. These reports will help you spot areas for improvement in your supply chain. And you can also track carbon generated by your supply chain and see its carbon footprint. This report serves as an objective measure to compare the effectiveness of different supply chain designs.
[If you are using SCM Globe Professional version, reports can be generated automatically by clicking on the “Generate P&L Report” button on the Simulate Screen]
See more about using simulation data to produce monthly P&L Reports in “Analyzing Simulation Data” – scroll down to the heading “Exporting Simulation Data“.
Carbon generation numbers are always changing as technology changes, so do a little research and see what you can find. Here are some basic estimates you can use to get started. These numbers are already entered as default values when you create new facilities and vehicles (the numbers are conservative and actual carbon emissions may be higher):
- Large Diesel Truck (110 m3) – 0.9 kg carbon per km
- Medium Truck (60 m3) – 0.7 kg carbon per km
- Small Truck (40 m3) – 0.5 kg carbon per km
- Train 40 ft freight container (65 m3) – 0.1 kg carbon per km
- Ship 40 ft freight container (65 m3) – 0.02 kg carbon per km
- Jet Airplane freight container (6 m3) – 1.2 kg carbon per km
Notes for Working with Case Studies

- Simulations are typically for 30 – 90 day periods. You can run simulations longer than that, but there is little reason to do so. This is because most companies do not run their supply chains unchanged for longer than 30 – 90 days at a time. Most companies use a 30 day S&OP cycle (sales and operations planning cycle), and these simulations correspond to that S&OP cycle. If you wish to simulate longer periods of time please see the online guide section “Tips for Building Supply Chain Models” and scroll down to the heading “Simulation Timeline”. If your simulation generates daily data for more than 90 days, it will start to overload the data download function. So use weekly data instead of daily data when simulating over longer periods of time.
- Products are usually defined as standard SHIPPING CASE or PALLET LOAD quantities, not individual items. For instance, if Product A is typically shipped in cases of 100 items, then define Product A using the price, weight and volume data for a 100 item case, not an individual item. Products can be defined in amounts equal to cases, pallets, or even 40 foot shipping containers. You would only define products as individual items if you were modeling a small supply chain in great detail.
- SCM Globe is used to model and simulate real supply chains so you can zoom in on the map and switch to satellite view to place your facilities exactly where they really are or where you want them to be. And all numbers in any model can be changed as needed to more accurately describe actual products, facilities, vehicles and routes. But when using simulations as a learning tool in a case study it does not make sense to change some default values even though the software will let you do so.
- Some Default Values in a Case Study Should Not Be Changed because it either doesn’t make business sense, or doesn’t make logistics sense. When working with case studies, don’t reduce product demand, and don’t reduce product prices – that makes no business sense (business is about increasing demand and profits). And don’t simply increase or decrease inventory on-hand amounts at the start of a case study – that makes no logistics sense (inventory doesn’t just appear or disappear).
- Distance and Time shown on routes is ROUND TRIP. If a route goes from a DC to a store that is 20 km away it will show a distance of 40 km because the delivery truck must travel to the store and back again (existing routes in some models may display one way distances but still use round trip in simulations – see workaround for Bug 1 in FAQs).
- Learn useful modeling techniques to help you build new supply chains and add new products, facilities, vehicles and routes to existing supply chains
- Download and Share Supply Chain Models — send a copy of your supply chain (json file) to other SCM Globe users.
Q&A VIDEO BOOK: Answers to Questions about Working with Case Studies and Simulations
These examples all come from the beginning case study, Cincinnati Seasonings. Work through the three challenges of Cincinnati Seasonings first. Then you will be ready to work on teams and take on more advanced case studies. Or you can start modeling and simulating real supply chains or designing new ones.
In an online Q&A session we got some good questions and demonstrated answers to those questions onscreen. Here are ten short clips with those answers. The title and description of each clip says what it’s about. You can start at the top of the playlist and the clips will play one after the other. Or just click on videos of interest.
- Online Guide and the 6 Steps to Get Started – quick intro to the “Getting Started” section of the online guide.
- Introduction to SCM Globe User Interface (UI) – there are only three screens in the simulation app; see what they do.
- My Account Screen– this is the first screen; it’s where you manage your account and your supply chain models.
- Truck Routing Question – Demonstrated Answer – see how to set the route, delivery frequency and delivery quantity.
- Simulating Supply Chain Models You Create – build your model then run it in simulations to see how well it works.
- Fixing a Problem in Louisville – Demonstrated Answer – see one possible way to get more product to Louisville.
- Realistic Supply Chain Model – see why “Cincinnati Seasonings” is a highly realistic supply chain model.
- Making Backup Copies of Supply Chain Models – supply chain models (.json files) can get damaged; make backup copies.
- Export Simulation Data to a Spreadsheet – you can export simulation data to your computer and a spreadsheet.
- Profit & Loss Reporting Template – get the P&L Reporting template and create reports using simulation data.
[If you are using SCM Globe Professional version, reports can be generated automatically by clicking on the “Generate P&L Report” button on the Simulate Screen]
You need answers to the 7 FAQs… There’s only 7… Please read the FAQs!
Adjust Your Computer Screen Resolution
Sometimes the display on the Edit or Simulate screen is so big you cannot see the entire screen; display graphs on the right side of the screen; or numbers overwrite the names of the facilities and you cannot read either the numbers or the names. This happens mostly on laptops. An example of this is shown in the screenshot below:
FIX THIS PROBLEM — Adjust the zoom level in your browser; set it to a lower zoom level. On the Chrome browser look in the top upper right corner of the browser and see three dots stacked on top of each other (in the Edge browser it will be three dots side by side, on Firefox it will be three short lines stacked on top of each other). Click on them as shown by arrow 1. A submenu opens up; see “Zoom” about half way down the submenu as shown by arrow 2. To the right of Zoom see your browser zoom level; if it is set to 100 or more try reducing it to 90 or less by clicking on the minus sign (-) next to the zoom number. Reduce the zoom level until entire screen displays in your browser.
Select the Language You Want for SCM Globe
Look in the upper right corner of any SCM Globe application screen to see the language selections. Click on the language you want to use in the application itself. You can also translate this online guide to any language by using the Google Chrome browser.
TRANSLATE THIS ONLINE GUIDE INTO ANY LANGUAGE using the Google Chrome browser. Right-click on any page to open the Chrome browser options window, and click on “Translate to…” — Google Translate window opens in upper right corner of screen — click on the three dots and choose a language.
AT FIRST you may feel a bit confused or overwhelmed as you start working with the models and simulations. But go ahead and jump in. It will get better as you go, and then it will “click”. It’s like learning the steps to a new dance – really awkward – then suddenly you get it – and it’s fun… 🙂 That’s how one professor describes it in What You Learn from Case Studies and Simulations.
[ Instructors interested in this case can request a free evaluation account and a copy of the study guide.]
You will acquire an intuitive or “street-smart” sense (a mental model) for how supply chains operate. And you will develop analytical skills for exploring different ideas to improve supply chain performance. In discussing simulation results with your instructor and classmates, you’ll find yourself using supply chain terminology and concepts you learned in readings and lectures to describe the problems you encounter and the actions you take to fix them. You will start talking and thinking like a real supply chain professional.
—>> Just ONE MORE Step… STEP 6 — The Seven Frequently Asked Questions (7 FAQs)!!!
STUDENT ACCOUNTS DEFAULT TO 90 DAYS from date of purchase – if your semester is a few weeks longer please send email to: info@scmglobe.com – tell us your semester end date and we’ll extend your account.
SAVE BACKUP COPIES of your supply chain model from time to time as you make changes. There is no “undo”, but if a change doesn’t work out, you can restore from a saved copy. And sometimes supply chain model files (json files) become damaged and they no longer work, so you want backup copies of your supply chain to restore from when that happens.
DOWNLOAD AND SHARE SUPPLY CHAIN MODELS to send a copy of your supply chain (json file) to other SCM Globe users.